Wire Cut Edm Process Pdf
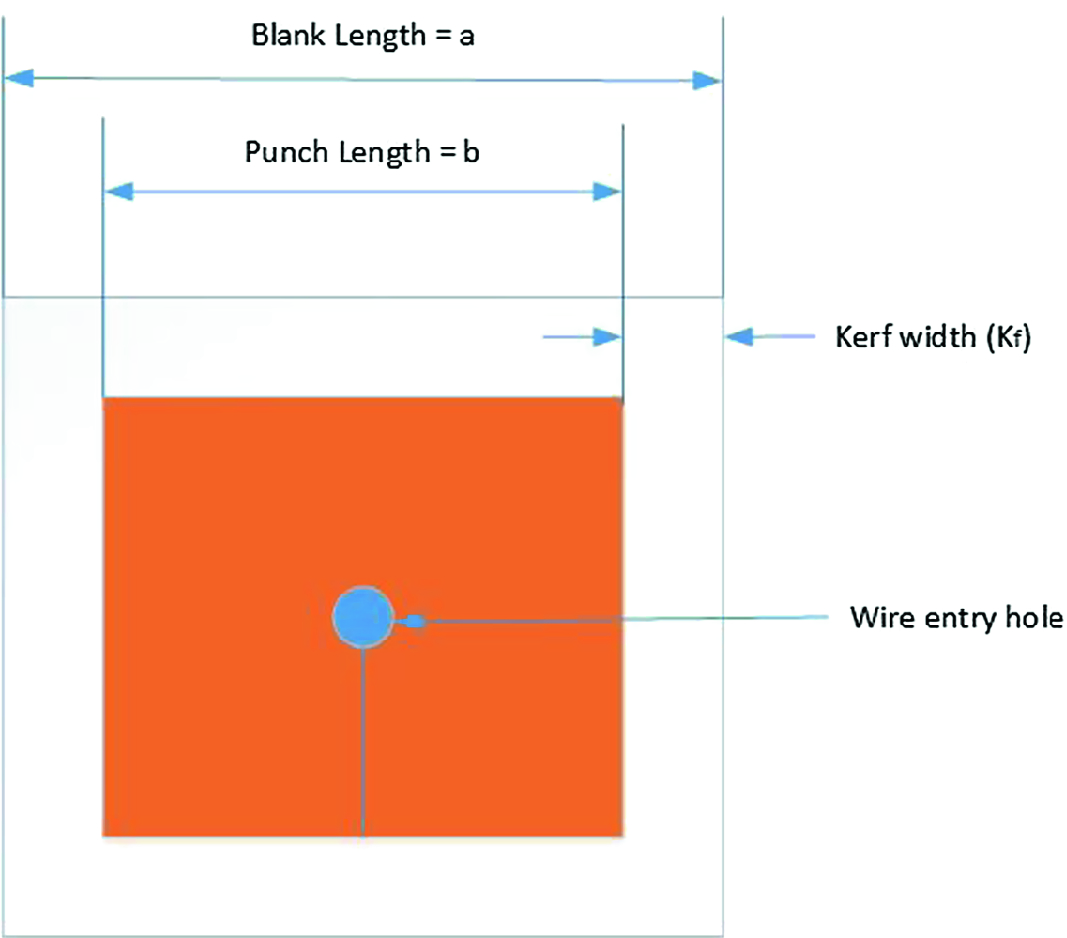
Wire edm fundamentals revolutionizing machining wire electrical discharge machining edm is one of the greatest innovations affecting the tooling and machining industry.
Wire cut edm process pdf. Wire edm is a non traditional machining operation in which complicated profiles are cut by the help of a wire by the application of heat produced from the electrical sparks. Wire electrical discharge machining wedm uses a metallic wire to cut or shape a workpiece often a conductive material with a thin electrode wire that follows a precisely programmed path. Electrical discharge machining edm also known as spark machining spark eroding die sinking wire burning or wire erosion is a metal fabrication process whereby a desired shape is obtained by using electrical discharges sparks. It was introduced in the late 1960s and has revolutionized the tool and die mold and metalworking industries.
Figure 2 1 shows various wire edm machines. To eliminate them skim cuts are used. Wire edm is also known as. It is probably the most exciting and diversified machine tool developed for this industry in the last fifty years and has numerous advantages to offer.
In wire edm thin single strand wire is used to cut the material from the workpiece. Some older wire edm machines used capacitors. Because of its versatility manufacturers use edm wire cutting machine operation for an extensive range of applications. However at our company reliable edm we have repeatedly cut carbide parts with a single cut.
Wire edm wire edm vertical edm s kid brother is not the new kid on the block. This process has brought dramatic improvements to industry in accuracy quality productivity and earnings. A constant gap is always maintain between the wire and w p. Influence of process parameters on the wire cut edm process the main goal of wedm manufacturers and users is to achieve a better stability of the process and higher productivity.
Because the process can cut very small pieces it is often an ideal choice for the production of small highly detailed items that would normally be too delicate for other machining options. Contact between the electrode and work piece. Wire cut electric discharge machining wedm laser beam machining lbm equipment of laser beam machining process parameters and safety issues. When precision carbide parts are needed then skim cuts are used.
Ultrasonic machining process usm ultrasonic machine and its process parameters. The wire is usually made of brass. Material is removed from the work piece by a series of rapidly recurring current discharges between two electrodes separated by a dielectric liquid and subject. The wire is continuously fed through the workpiece submerged in a tank with dielectric medium.
The wire is usually made of brass or stratified copper and is between 0 1 and 0 3 mm diameter. Wire cut edm applications.